“Starting from scratch, we innovate our innovations in pursuit of original sound quality.”
The story behind the development of the SZ Series
The successful launch of the FXZ series of inner ear headphones has been followed by the long anticipated debut of the SZ series around ear headphones. We interviewed Takuji Miura and Yuji Yanagishita, the two developers responsible for redefining the premium quality for JVC’s high-end around ear headphones.
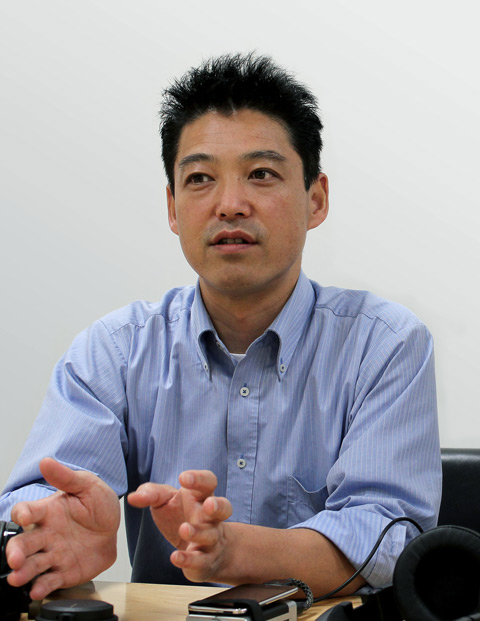
Yuji Yanagishita
Manager
Engineering Operation Audio Div.
JVC KENWOOD Corporation
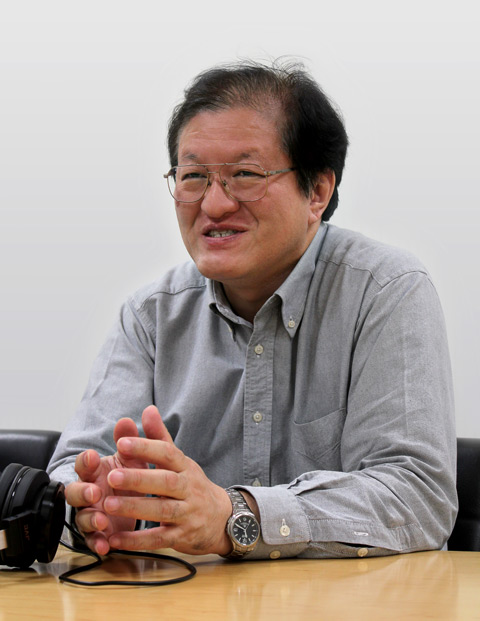
Takuji Miura
Senior Adviser
Engineering Operation Audio Div.
JVC KENWOOD Corporation
“Real Sound System”-equipped Around Ear Headphones Arrive!
When did you start the development of the around ear headphones?
Miura“From the beginning, we had considered incorporating the Real Sound System in both the inner ear and around ear headphones. More specifically, our development of the around ear headphones started in the fall of 2011 just when the basic development for the FXZ series of inner ear headphones was completed.”
So you just went on to next development project without a break. Which project posed a bigger challenge, the development of the inner ear headphones or the around ear headphones?
Miura“That is not easy to answer because each involved very different elements. Though both shared the same sound quality goal, we struggled to overcome different aspects. The biggest issue faced with the inner ear headphones was figuring out a way to fit the complex mechanism in such a small space. On the other hand, the around ear headphones have ample space in comparison with the inner ear headphones, but the mechanism of the Real Sound System is extremely dense and intricate, and condensing this package into a compact form gave us a few headaches. Moreover, the HA-SZ around ear headphones series was also scheduled for product commercialization in a slightly higher price range, and customers naturally would expect a corresponding improvement in audio quality. That meant that right up to the moment the product finally entered production, we were endeavoring to raise the audio performance.”
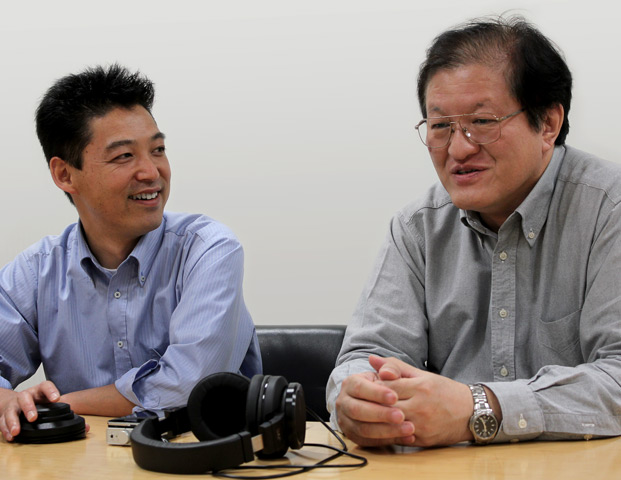
Freedom of Design Raises the Bar of Difficulty.
What specifically are the aspects you had difficult time with?
Miura“Ordinarily headphones reproduce sound using a single full range driver unit, but the Real Sound System adopts multiple drivers. For the SZ series, we chose to use two units: the bass unit (55mm in diameter) and a mid-to-high range unit (30mm in diameter). While these conditions gave us a high degree of design freedom, it also presented some pitfalls. You see, a broad range of freedom also means many more parameters to decide. We also chose to incorporate the Double Bass Reflex system in addition to the Kelton speaker design method in the new series. This necessitated four chambers: one behind and two in front of the bass unit, and one behind the mid-to-high range unit. We had to determine the capacity of each chamber. What kind of balance should we target for the overall system? Since we had no development precedent that we could refer to, we had to start development from scratch. Relying on intuition and experience, everyday we faced the sobering task of repeated trial and error. Of course, simulations allowed us to predict outcomes to a certain degree, but the final decisions could only be made after repeated testing and auditions. The final prototype turned out to be double the size of the finished product. At that point, we met our biggest challenge: condensing the size of the system while constantly refining the audio quality.”
The SZ series headphones are a sealed “closed” type. What is the reason behind that choice?
Yanagishita“Many people use their around ear headphones in their homes, but we wanted our users to enjoy the great sound of the Real Sound System not only indoors, but also outdoors. That’s why we chose to make it a closed type so there will be no sound leaks. “Superior models from overseas are often open types these days, but they are susceptible to sound leakage. If there is sound leakage from the headphones, that means that sound can also comes from outside. Although open types may give the user a sense of liberation, our focus was the delivery of realistic sound quality by the Real Sound System in this model. That is one of the main reasons for adopting the closed type design.”
Newly Designed Woofer Is the Largest Ever (55 mm in diameter). Quality Audio Experience Born from the Pursuit of Bass Excellence.
We understand that you listened to the female jazz vocals during the development of the inner ear headphones. What did you listen to this time?
Miura“Yes, and I listened to jazz vocals again, but that was not all I listened to (laughter). The music we audition during testing varies depending on the person in charge of design, but we believe listening to the type of music we like or usually enjoy enables us to better detect changes. “We wanted to make headphones that let our users to experience even the subtlest textures and nuances in the sound of musical instruments. If we wanted to simply boost the bass, it would not be so difficult. However, producing bass that has superior resolution, definition and dynamic range, well, that is quite difficult. In the case of inner ear headphones, the bass is sensed only inside the ear, but the around ear headphones have space around the ears so the whole ear feels the sensation of the bass. These sensations will be quite different from the experience delivered by the inner ear types, and the sound tends to have livelier feel to it. Many times during testing, when I used the prototype to listen to music that I had previously thought had a lot of bass, I was amazed to discover that I was hearing, not an overwhelming volume of bass, but instead a deeper more profound quality of bass in the song.”
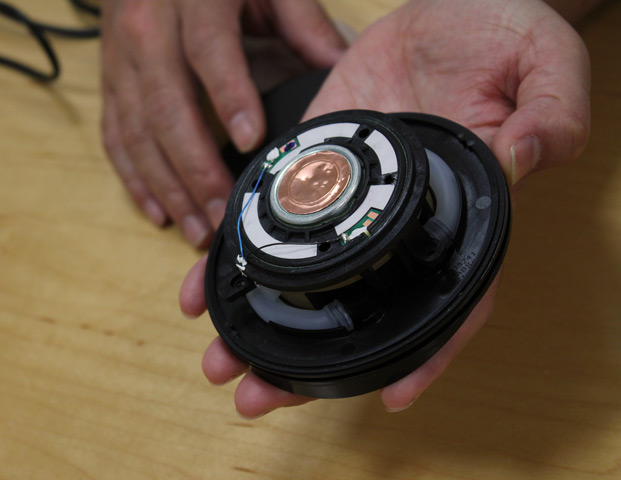
So these are not headphones for bass enjoyment?
Miura“At the product launch press conference, we were asked that question, and we responded that our aim was crisp clarity across the entire audio range - high fidelity reproduction of not only bass, but also the mid-to-high range. That is why we have achieved a product that reproduces music with a “live” quality and can let you hear even the smallest breath of the performer.”
The bass unit of the SZ series is huge, measuring 55 mm in diameter.
Yanagishita“The larger the surface area of the diaphragm, the greater the capacity of the unit to effortlessly produce bass. That is why we chose to use a newly designed woofer with a diameter of 55 mm. This is the largest woofer for headphones in the history of JVC. However, headphones, of course, are worn on the head, so simply making them bigger and adding weight detracts from the experience. We had repeated discussions on what is the ideal balance of these and other factors before we came to a decision.”
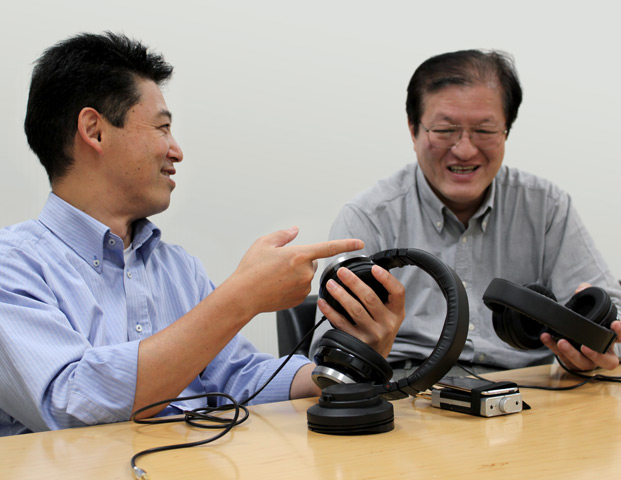
Dual Stream Ducts deliver realistic deep bass sound to the ears.
The long, thin Stream Duct is a defining feature of the FXZ series, but the Dual Stream Duct in the SZ series is also quite impressive.
Miura“In the initial development, we used the Kelton speaker design method and tried a single chamber and a single duct. It produced not only good bass sound, but also undesirable mid-to-high range frequencies from the woofer. Of course, this was unacceptable, and we began studying many alternatives. There was the choice of solving the issue electronically by using a crossover network circuit; however, the few components available were huge, so we determined that the answer was an acoustic solution and we began working on the shape of the duct. We attempted making a long, large-diameter duct that was wrapped around the unit. The resulting acoustics were not too bad, but the idea was dropped because the product would be ridiculously large (laughter). In the end, we adopted the double bass reflex method with two air chambers in front and installed two ducts for the output to achieve sufficient duct cross-sectional area to deliver a rich bass quality.”
The HA-FXZ Stream Duct is made of stainless steel. What did you use for the Dual Stream Duct?
Yanagishita“HA-FXZ inner ear headphone series required a thin, long duct that could be bended. If soft materials were used, the acoustic channel could be crushed during the bending and installation of the duct. That’s why we chose stainless steel.
“In the case of SZ series, it would be necessary to install the duct inside a space filled with various components and cables. In order to prevent resonance arising from contact with those components, we adopted the silicon rubber.
“As a result of this choice, we achieved good attenuation of sound from the bass unit with more than 300Hz accompanied by high quality bass reproduction. At the same time, the output of the mid-to-high range unit was tuned for distortion-free clarity by optimizing the capacity of the back cavity to cut off frequencies under 300Hz and by tweaking sound absorption characteristics and magnetic strength. In other words, we are extracting only the best from the two units.”
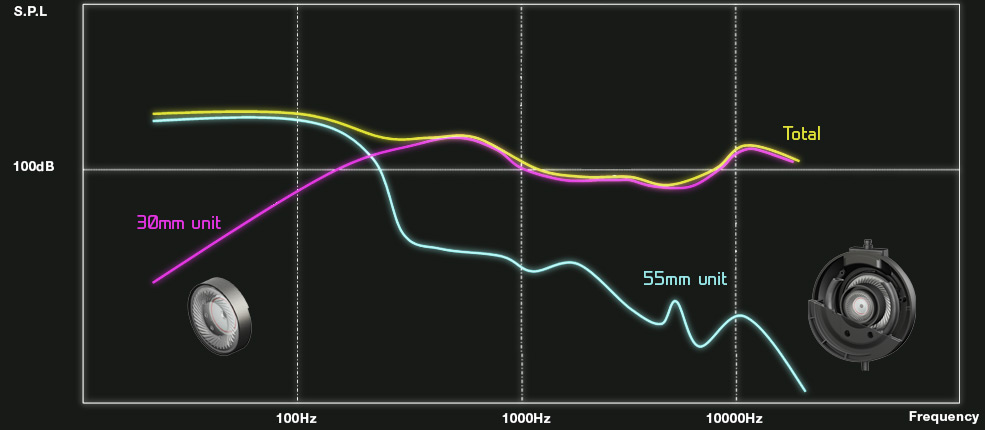
The quest for premium sound quality means uncompromising attention to the last detail.
Any interesting behind-the-scene stories?
Miura“I am not really sure if this qualifies, but as you know, the HA-SZ2000 is positioned as a premium model. With this in mind, we adopted a brass vibration damping cylinder to enhance bass separation and audio reproduction clarity. Also we chose silver-coated OFC (oxygen free copper) cable to improve the resolution not only the mid-to-high range but also the entire audio range for vividly clear sound quality. However, despite all these features, I felt that something was missing from this premium model. In the very end of the development, just before it was too late, I looked at the steel material used in the magnetic circuitry of the driver units. Ordinarily steel components are cold pressed - punched out of steel sheets without applying heat. They are fabricated with brute force, so to speak. At the molecular level, you can see that components are structurally riddled with deformations that have a negative impact on the sound. We decided to apply heat treatment to the steel used in the magnetic circuitry of the HA-SZ2000. Heat treatment at temperatures reaching near 950 degrees Celsius followed by gradual cooling lasting over a day ensures that the molecular structure was relatively free of deformation. With the adoption of heat treatment, my last concern disappeared, and I could state with confidence that our product reproduced premium audio quality. Because efforts like these came so close to the end of development, they did not even make it into the product brochures (laughter). Despite that, I am glad that we never gave up on seeking improvements until there was no more time at all.”
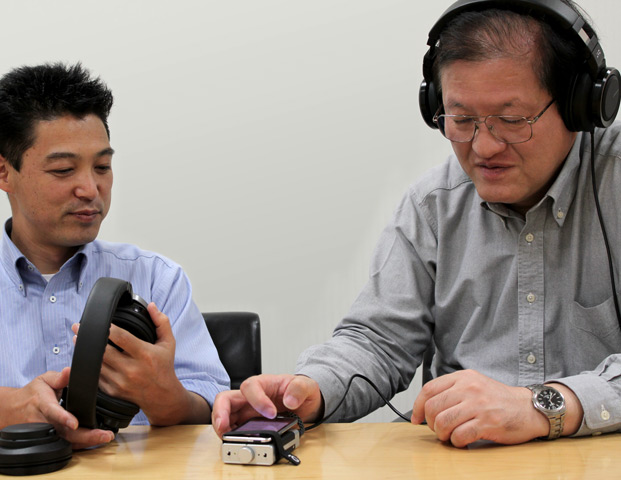
So you were uncompromising in every detail up until the last minute.
Miura “We also struggled with sound leakage. The process of product development involves not only the developers themselves. People in other departments from project planning to marketing also participate in our prototype trials. One time when we developers had thought we had everything covered, those others let us know that they were concerned about some sound leakage that occurred depending on the type of music and also the volume of sound. It was quite a last-minute challenge.
“The vibration of the headphone diaphragms generates sound. If the headphones are totally sealed, air movement is inhibited, preventing the generation of bass. When we allowed a little flow of air, we found it was the source of mid-to-high range leakage. We thought up a variety of ideas, but our final solution was the installation of two hidden ducts in the rear that cut off the mid-to-high range leakage that was found to be annoying.”
Driven by innovative application of speaker theory, headphone evolution goes on.
The degree of application of acoustic theory came as quite a surprise. In so many ways, this development project was a series of “first ever” technology challenges for your team.
Yanagishita“The SZ series presented our engineers with challenges that we were truly eager to meet. From the beginning, there were no rules, which is both a pleasure and a pain for engineers. Since we had no precedents to look at, we had to start from scratch and build on those efforts. We carefully documented data throughout the entire process, but many unquantifiable elements also impact the outcome. In the end, we had to rely on qualitative evaluation - our ears - to finish the product.”
The Real Sound System is a successful example of the application of speaker theory.
Miura“I have spent over 30 years as a speaker engineer, so for me, the sound that comes out of the speaker is something that I create. I had always wanted to create headphones that could reproduce the same audio quality that comes out of large floor model stereo speakers. Great audio from speakers requires consideration of the room in which they are enjoyed. In addition, it is generally not possible to turn up the volume of speakers in ordinary homes and enjoy their full potential. Headphones, on the other hand, let you listen to any music you like and as loud as you want, anywhere without concern about bothering others. For me, the headphones are the best way to listen to great audio. Our new headphones are inspired by my experience in building speakers based on the Kelton speaker design method and the Double Bass Reflex system. I believe there is still much speaker theory that can be exploited in the development of future headphones. Naturally we do not set out to do something new. Our objective is always the ‘pursuit of original audio quality’. I look forward to meeting more new challenges in the course of our quest to achieve this goal.”
It looks like there will be no end to the pursuit of original audio quality at JVC. We look forward to even more exciting developments from your team in the future. Thank you very much.