Challenge after challenge in the relentless pursuit of original sound.
The story behind the development of the FXZ series headphones.
Learn more about the breakthroughs that led to the achievement that rocked the audio world, in this interview of Takuji Miura and Shinji Tamura, the lead developers of the FXZ series of inner-ear headphones and creators of the innovative “Real Sound System” architecture featuring the amazing Stream Woofer concept.
Takuji Miura
Fan of Female Vocalists
Senior Adviser
Engineering Operation Audio Div.
JVC KENWOOD CorporationShinji Tamura
Fan of UK Rock Music
Engineer
Engineering Operation Audio Div.
JVC KENWOOD Corporation
JVC Inner Ear Headphones rock your world with a stream of “Industry Firsts”.
JVC seems to produce an endless stream of innovative concepts and “industry firsts”. What is the driving force behind your development?
Miura”Pursuit of original sound” is our philosophy. We want to reproduce music with the fidelity and dynamic quality that makes you feel you are there, listening to a live performance, even with small headphones. We refine and innovate technologies through trial and error in our search for architecture and materials that make this a reality and studying the challenge from a variety of angles. We do not set out to be the first in the industry or the world from the onset. Ultimately as a result of our pursuit of original sound, we end up creating technologies and producing products that are the first of their kind in the industry and the world.”
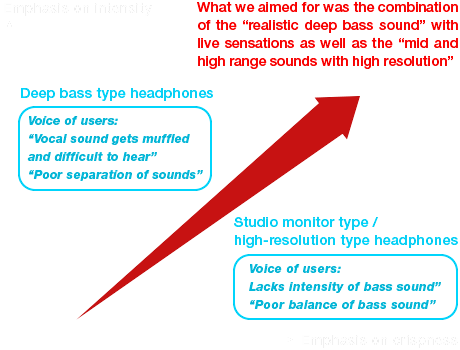
“With the high audio resolution and realistic bass of the FXZ series, you can hear the difference between a wood bass and electric bass guitar.”
JVC followed the FXT90 headphones incorporating the Twin System Unit with the development of the “Real Sound System” and a brand new architecture.
Miura“Our development staff had months of heated and repeated debates over what should be our next step. Some even suggested that our twin system should obviously be followed by a triple or even a quadruple system. However, we finally concluded that the direction of our future development should be decided by listening to our users – figuring out what quality of sound they desire. What we heard was that inner-ear headphones in the past that featured deep bass suffered from muddied mid to high frequencies, making it difficult to get decent vocal sounds. On the other hand, so-called studio monitor types delivered high resolution, but lacked in the intensity of the bass sound.”
So you went back to the basics and developed a new product from scratch.
Miura“That’s correct. We often ask ourselves, ‘Can we clearly hear difference between a wood bass and an electric bass guitar?’ Conventional deep bass-type headphones deliver volume in the low range, but often without quality. It is possible to tune a single unit to deliver bass sound, but at the expense of the mid range sound or with insufficient high range. We simply did not want to create anything like that.
“In terms of sound frequencies, hi-fi audio headphones must not only reproduce deep bass sound, but also deliver the mid and high range. We did not want to provide a product that merely emphasized a segment of the frequency range. We did not set out to develop deep bass headphones, but rather headphones that deliver clarity across the entire frequency range - so clear that the difference between a wood bass and an electric bass guitar can be easily distinguished.”
So how did you put it all together into a product?
Miura“First of all, we decided to use at least two units, instead of just one. We needed to produce the mid-to-high range with crispness and to deliver the bass range with depth. We did not want a bass range unit with flat frequency characteristics. We wanted to have a subwoofer unit that cutoff the mid to high sound range, and combine it with a unit for the mid to high sound range. This would eliminate interference and distortion in the mid to high range and achieve our goal of lively dynamic sound throughout the entire range.
“The difficult question was how to actually realize this concept. You see, no dynamic-type headphones had ever incorporated a subwoofer before.”
So with no precedent to follow, you had to think up a solution from scratch.
Miura“We wanted to eliminate the upper segment of the woofer bandwidth to avoid the interference between the overlap of bass output and the sound produced by the mid to high range unit. There are two approaches to achieving this. One is to cutoff the undesirable frequency electronically. A network, so to speak. This could be achieved by inserting a coil. Our targeted cutoff point for this product was 100Hz, but when we calculated the capacity of the coil required to achieve this, we realized that it had to have an amazingly large capacity of 38mH.
“No coil with a capacity of 38 mH is available as a component in the world. The upper limit for chip components is probably about 1mH, which means it would be possible to cut off only to about 4kHz. So in our initial studies, we gave up looking for an electronic solution. That left us with only an acoustic means to achieve our goal.
“However, there is a limit to how long you can make a conventional duct in the limited space of the inner ear headphone housing. Probably only few tens of millimeters at the most. So our next question is how small the internal diameter needs to be? Well, our calculations revealed that an internal diameter of few millimeters is by far insufficient. No, we had to make it a small fraction of a millimeter.”
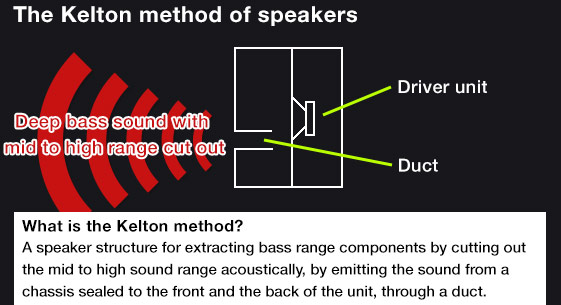
Can sound come out of a duct that has a diameter measuring only a fraction of a millimeter?
Miura“That was a structure we have never seen before, so we really were not that confident that it would work. “As an acoustics specialist, minimizing acoustic resistance in the design of inner ear headphones is fundamental. The sound path of sound must be as big as possible. The surfaces must be made as smooth as possible. If any bends in the path, then they must not be acute angles. Bends should be as gentle as possible. Our desire to make the duct as narrow and long as possible is just the opposite. We had never done anything like this before and certainly would not think of pursuing this approach in the first place. However, theoretically, this was exactly what we needed to do; otherwise, we would have no bass output. So we decided to test the concept by making a prototype.”
Well, this (the prototype) certainly is unique!
Miura“A person wearing this prototype looked like a classic space alien. It gave our staff quite a laugh.
“When we actually examined the data from our experiment; however, we were pleasantly surprised to find quite good delivery of the bass range. In terms of frequency characteristics, it was dropping off cleanly at 100 Hz.
“We were also getting good acoustic pressure. We realized that by applying this architecture to a subwoofer, we were on our way to creating the targeted product. Of course, the prototype was a proof of concept and could never be released as a product as it looked. At this point, we faced the second hurdle: the hard work of product commercialization.”
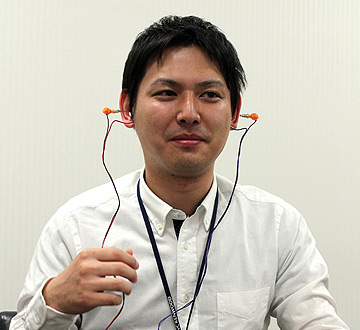
Product designer Shinji Tamura wearing the prototype.
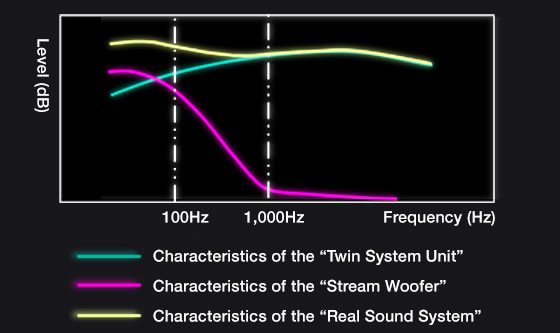
“Our challenge: Making the three units and a 30mm-long duct as compact as possible to fit in an inner-ear headphone?”
I understand that product commercialization was mostly the responsibility of Mr.Tamura.
Miura“That is correct. At this point in the story, Mr.Tamura took over the struggle.”
Tamura“With the basic architecture decided, it was time for me to work with the product designer, starting with studying the specific issues of translating the prototype into a commercial product. The most significant issue was how to accommodate this long duct. We wanted to use as large a diaphragm as permissible for bass output from the subwoofer unit, so we adopted a unit with the diameter of 8.8 mm – the maximum size for wearable inner-ear product. However, our planned placement of the large unit behind the Twin System Unit would make wearability poor. We had to figure out how to resolve that.”
So even though the audio quality issue was solved, you still had to agonize over how to fit the long duct solution in the product?
Tamura“That’s right. It seemed that wrapping the unit around the circumference of the unit would be the best way to go. However, since the internal diameter of the duct needed to be so small, the question was what material to use. The only commercially available small diameter tubes that we could find were either silicon tubes for medical applications or what looked like needles for syringes. Figuring out how to bend it without crushing the internal diameter of the duct was also a significant issue. If it had not been hollow, we could easily force it to bend. However the hollow core meant that the internal walls could be badly deformed or crushed together, resulting in blockage or restriction of the channel and preventing sound output.”
Miura“We decided to use stainless steel instead of silicon. There are two reasons. The first had to do with the size. Silicon required thicker walls, which resulted in a larger external diameter of the duct, which in turn makes the overall size of the inner ear headphones larger. We of course wanted to keep the product size as small as possible. The other issue had to do with manufacturing. If we used silicon, it was potentially possible that the internal walls of the duct could be crushed together by accidental bending during the assembly of the product. Considering these issues, we decided to tackle the challenge of using stainless steel although processing would be difficult. In fact, the manufacturing plant kept telling us that our design was impossible. In the end, we had to make repeated visits to their offices to beg them to accept the challenge, and finally succeeded in realizing the component.”
What other aspects were difficult for you?
Tamura“The Kelton speaker design method requires the sealing of the unit in the front. We racked our brains seeking a way to seal in the unit. We did not want to increase the number of parts in the product. Increasing the number of parts leads to an increase in weight, which then impacts on what it feels like to wear the product in the ear. Every problem fix seemed to lead a new problem. (laughter). “We wanted to seal it with some simple wrapping, but it is necessary to seal the subwoofer with a metallic material to improve the quality of the sound. I consulted Mr.Miura, and he insisted that metal must be used. So we decided to use a metal part. The diameter of the subwoofer unit is large and the diaphragm also experiences significant movement so a metallic part is necessary to hold it in place.”
“Until it is truly ‘wearable’ and comfortable for the user, it is not a product.”
So you finally saw the light at the end of the tunnel of product commercialization.
Tamura“Yes, once we got to this point, the issue was how to assemble all these many parts. We had to fit three driver units into a product form that would fit in the ear without sacrificing the user comfort.”
So how in the world did you proceed?
Tamura“We fabricated models using laser beam lithography and had our colleagues actually wear them and then share their impressions. We went through about 20 different designs, and we finally settled on an arrangement with the Twin System Unit facing directly into the ear and the subwoofer unit vertically oriented.”
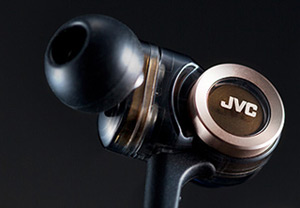
So the distinctive form of the product is the result of repeated trial and error?
Miura“I don’t believe you can find another product in which three units plus a stream duct has been packed in such a compact form.
“Preserving the high fidelity of the mids and highs by cutting off upper end of the bass output and powerfully and discretely producing realistic bass, this product is a masterpiece that we are confident will deliver an audio experience that boasts both superb resolution and solid bass. Our uncompromising attitude also extends to the design aesthetics. This aspect did not move forward until we reached a consensus on the concept among all the development staff members.”
Both the form and the performance are definitely revolutionary.
Miura“The FXZ’s Twin System Unit is actually completely different from one in the FXT90. Our initial FXZ development used the same Twin System Unit in the FXT90, but once we achieved sufficient bass range, the mid-range sound just did not measure up dynamically. We decided that it was unacceptable, and redesigned practically all the parts.”
Tamura“Our aim was to create a sound that had much, much more resolution in the mid to high acoustic range, so we adopted a thin film and lightweight carbon nanotube diaphragm for the Twin System Unit. We were able to reduce weight by about 20% compared with the FXT90.
“We also used a stronger neodymium magnet to enhance audio response. Enhanced magnetic strength also tightens the lower end of range of the Twin System Unit, but this slight reduction lower frequency compensation does not pose a problem because the subwoofer is available to produce the bass range.
“We also changed the metal unit base material from copper to brass, which has a higher specific gravity, to ensure that the movement of diaphragm does not overwhelm the base’s ability to control it. The metal unit base of the FXT90 is fabricated by pressing, but the FXZ series metal unit base is manufactured by precision metal cutting machines. They may not appear different from the ones in the FTX90, but they have evolved into something completely different.”
From planning and development to mass production, the challenges faced by developers continue.
I understand that you continued to face a lot of difficulties not only during the development stage, but also after the product entered production.
Tamura“Naturally I was involved in the preparation stages of production, but I was also constantly present on the line once we began production to confirm quality consistency. Because this product required the assembly of a large number of parts, it was quite challenging for our production staff.”
Miura“There are worries until the development is completed, but then there are new worries until product commercialization is done. Finally it is quite difficult to get the product into production and to keep the delivery deadlines.”
The phenomenal inner ear headphones developed by a fan of female vocalists and a UK rock lover.
When “tuning” the audio performance of a product in development, what kind of music do the developers listen to?
Miura“We listen to a variety of genres when we are tuning the audio performance. We listen to full orchestras playing classical music or a pipe organ playing church hymns to confirm appropriate depth and realism of the bass. Outside of work, I enjoy listening to female jazz vocalists. I am especially a fan of Sophie Milman, and I was listening to her a lot when I was involved in the development of the FXZ series headphones. I adjust the balance between the wood bass and drum kicks with the vocals and piano. I tune the performance so that even if the deep bass of the wood bass or drum kicks are present the clarity of the vocals is unmuffled.”
Tamura“I mostly listen to UK rock music. I used to listen to Oasis often during the development of the FXZ series headphones. Otherwise I used the audio sources available for sound checks from the JVC recording studio (Japan).”
So with the FXZ series headphones, I can enjoy the both fine nuances of a female vocalist and a powerful rock beat and bass!
Tamura“Yes, but if you have an opportunity to get a hold of the FXZ series headphones, please try them out by listening to your usual music choices. I am confident that the music you’ve been enjoying will sound new and different. You will be pleasantly surprised to hear how the headphones reveal subtle sounds that you did know were hiding in the music.”
The never-ending evolution of the JVC inner ear headphones.
Miura“The FXZ series is remarkable, not only because it features 3 driver units, but also due to the extensive array of technical and acoustical innovations. The most important feature is how our development of the stream duct cuts off the frequency characteristics of the subwoofer at 100 Hz., We put every innovation we can think of into the development of this series at this point in time. However, if I were asked if it scores 100%, I would probably have to say that there is more we can do. The inner ear headphone is a recent product with a relatively short history, and is still in the middle of development. We believe that there is still a long road of development ahead of us.”
We look forward to new developments from your team in the future. Thank you very much.
(Interviewer: FXZ Series Special Site Editorial Office)